UV Led curing in electronics industry.
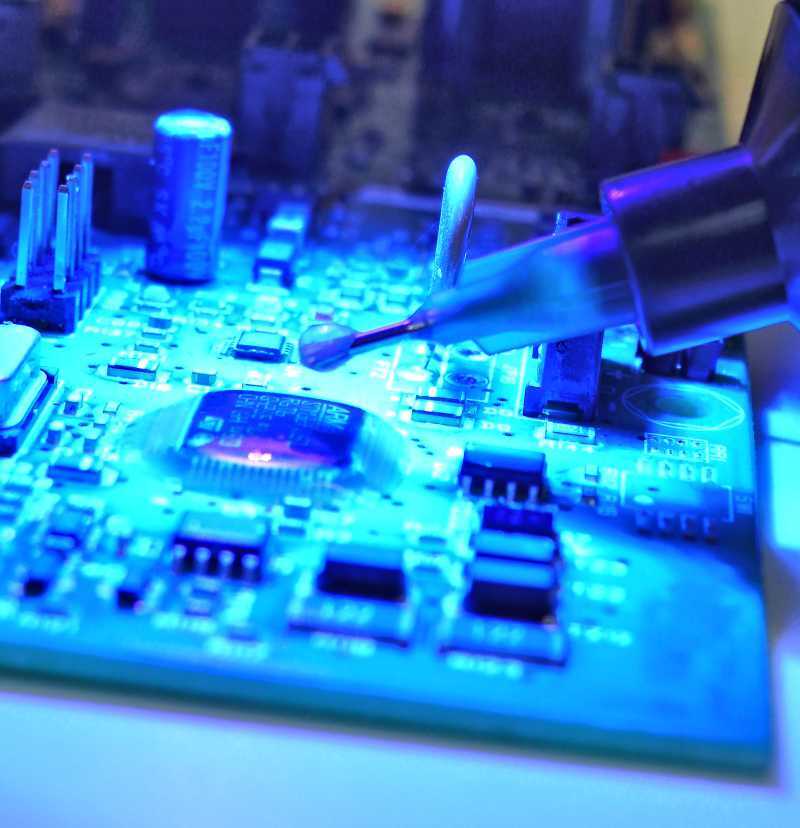
UV LED curing is a process used in the electronics industry to quickly cure adhesives and sealants using ultraviolet light.
Applications
This technology is particularly useful in applications such as bonding components, potting, and encapsulating electronic parts, providing strong and durable bonds that enhance the reliability of electronic devices.
- Component Bonding: Used for bonding various electronic components, such as sensors, connectors, and circuit boards.
- Encapsulation: Protects sensitive electronic parts from moisture, dust, and mechanical damage.
- Potting: Filling enclosures or cavities with adhesive to secure components and provide insulation.
- Sealing: Creating airtight and waterproof seals to protect electronic devices from environmental factors.
This technology offers several advantages:
1. Speed: UV LED curing can significantly reduce curing times compared to traditional methods, allowing for faster production cycles.
2. Energy Efficiency: UV LEDs consume less energy than traditional UV lamps and produce less heat, which is beneficial for heat-sensitive components.
3. Precision: The focused light from UV LEDs allows for precise curing in specific areas, reducing the risk of affecting surrounding components.
4. Reduced VOCs: Many UV-cured adhesives have lower levels of volatile organic compounds (VOCs), making them more environmentally friendly.
5. Versatility: UV LED curing can be used with a variety of materials, including epoxies, acrylates, and silicones, making it suitable for different applications within electronics.
Benefits in Electronics Manufacturing
1 High Bond Strength: UV-cured adhesives often provide excellent bond strength, which is critical for electronic components that may experience mechanical stress.
2 Transparency: Many UV-curable adhesives are clear, making them ideal for applications where aesthetics matter or where the adhesive needs to be invisible.
3 Chemical Resistance: UV-cured adhesives typically exhibit good resistance to chemicals, moisture, and temperature fluctuations, which is essential in electronic applications.
4 Low Shrinkage: This minimizes stress on components during the curing process, helping to maintain the integrity of the electronic assembly.
Curing Equipment
Proper UV LED curing equipment must be used to ensure effective curing. This includes the right intensity and wavelength of UV light.
If you're considering using UV LED curing for a specific application or have more questions about the technology, feel free to ask!
https://www.photoel.com/en

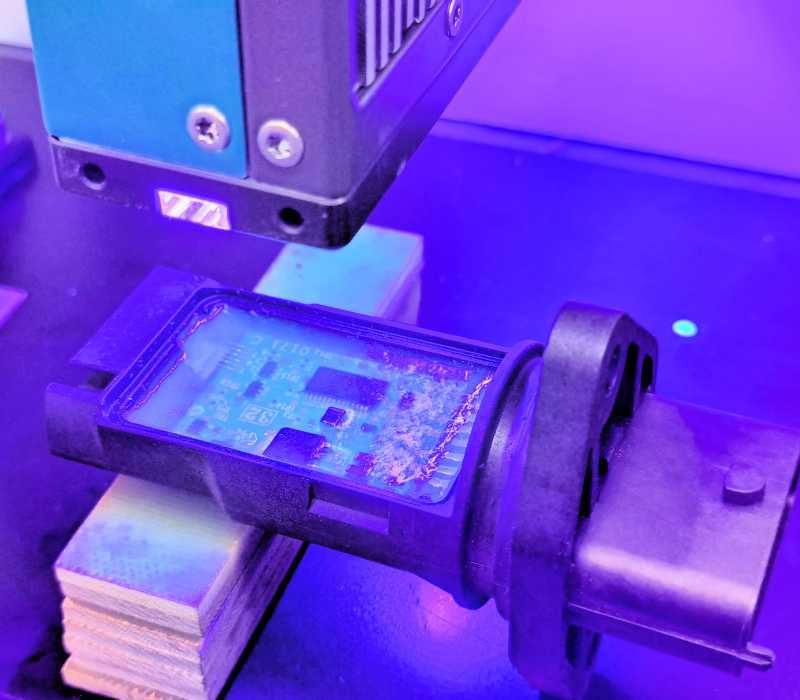
